近年、ITを活用したデジタル化に取り組む企業が増えていますが、取り組みに成功している企業のほとんどが社内にエンジニアを抱え、潤沢な予算を抱える大企業ばかりです。
デジタル化を実現するにはシステム開発が必須であり、社内の業務課題を解決するシステムを用意する必要があるため、エンジニアの存在が不可欠ですが、中小企業にエンジニアが在籍するケースは稀であり、そもそもITリテラシーの高い人材が不在というケースがほとんどです。
そのため、デジタル化の実現は社内にITエンジニアがいる、もしくは潤沢な予算でシステム開発会社に依頼ができる企業だけの領域で、中小企業には到底実現できない領域だと考えられていますが、「エンジニアなし、予算なし」の状態でアイディアのみでデジタル化を実現し、大幅な業務効率化に成功した中小金属板金加工業社が存在します。
この記事では、エンジニアなし、予算なしの状態からITツールの組み合わせでデジタル化に成功した株式会社曽我製作所のデジタル化事例を紹介します。
曽我製作所におけるデジタル化の道のり
曽我製作所株式会社は神奈川県厚木市にて、自動車部品製造及び板金加工を行なっており、大手自動車メーカーのフレーム部品を製造するメーカーを主要顧客とする板金加工会社です。
「人の力に頼らず「NC化」をする」を経営方針として掲げ、数年ごとに最新の設備投資を行うだけでなく、現場の職人さんのノウハウを蓄積するデジタル化の仕組みを独自構築することで、最新設備とデジタル化による付加価値の高いモノづくりを実現し、自動車部品以外の様々な分野に価値を提供する挑戦する「創造挑戦型企業」となっています。
今でこそ、曽我製作所の業務はデジタル化によって、効率的な業務形態となっていますが、数年前までは製造業中小企業における共通の悩みである「紙業務」に大きな課題を抱えていたのです。
導入前のアナログ業務
製造業中小企業において「紙業務」はどの企業にも存在する共通の課題であり、曽我製作所も「紙業務」による非効率な業務形態の真っ只中に位置しており、以下のような課題を抱えていたのです。
- 紙の山から図面や作業要領書を探す
- 経験の少ない新人は常にベテランの職人に何度も質問をしている
- 作業をする人間が変わると、生産効率が大きく異なる
製造業の現場において最も重要となるのが時間当たりの生産数であり、生産効率が悪ければ、製品における製造原価が高くなることはもちろん、他の仕事に着手できないため、工場の稼働率低下に繋がります。
紙業務の存在で、曽我製作所の現場には様々な無駄な作業が発生しており、現場作業者にとって作業負担の多い業務環境となっておりました。
現場に多くの課題が潜んでおり、生産性を阻害していることを認識しながらも、曽我製作所の社内にはITに詳しい人材が在籍しておらず、「何から手をつければいいのか」という状態が続いていたのです。
デジタル化のきっかけ
曽我製作所がデジタル化に着手するきっかけとなったのは、作業員ごとの習熟度のバラつきと加工作業前に必ず行われる探す時間の存在です。
デジタル改革前の新人教育の現場では、指導者が口頭で加工方法などをレクチャーしていましたが、1回で覚える人と何回も聞かないと覚えられない人、メモを取る人と取らない人が混在したため、結果として技術の習得度合いに大きなバラつきが生まれていました。
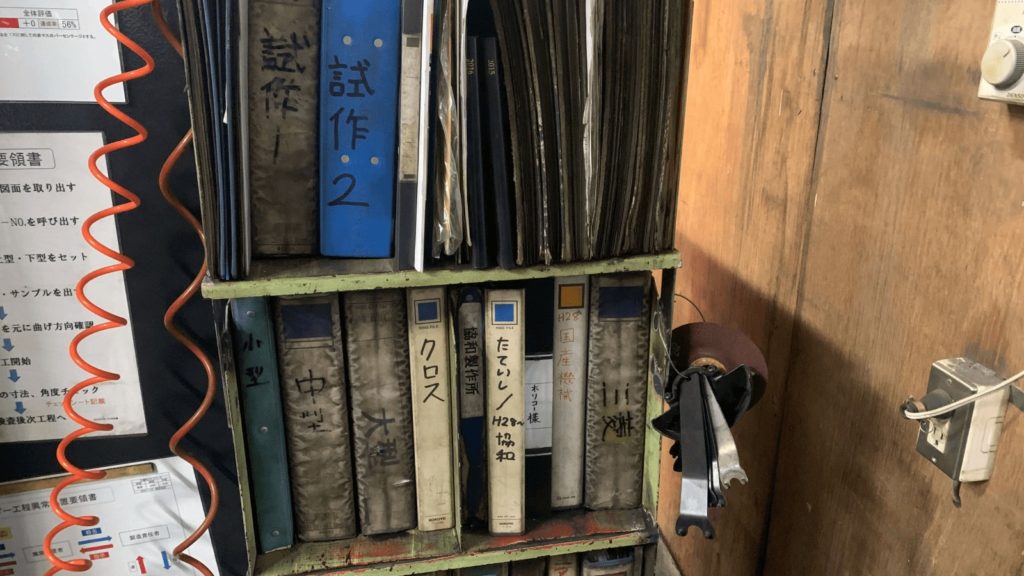
また、情報が一元化されていなかったため、作業する度に必要な図面と作業手順書を紙の山から探し出す必要があり、現場には本来やらなくていい無駄な作業が発生していたのです。
製造業の現場において、最も重要なのは製造原価を低減することであるため、現場ではいかに効率的に作業を行う生産数を増やす必要がありますが、曽我製作所では習熟度の影響で作業員ごとに作業スピードが大きく異なり、作業前の情報を探す時間が現場の生産性を大きく阻害していたのです。
「作業の習熟度は人に依存するものであり、人を根本的に変えるのは難しい」「紙だらけの製造現場においてどうすれば簡単に情報を調べられるか」と頭を抱えていた状態でしたが、ひょんなことで目にした全く製造業と関連のない料理レシピ検索アプリからアイディアを見出したのです。
日本の20代から40代の女性を中心に月間5700万人以上が夕方の時間帯に必ず利用しているのが料理レシピ検索アプリ「クックパッド」です。
ユーザーはアプリの検索画面で作りたい料理の名前を打ち込むだけで、料理をするために必要な情報の全てを簡単に集めることが可能になります。
クックパッドの普及前は、主婦には曽我製作所の現場と同様に探す作業が存在し、毎回調理を始める前に料理本を開いて、必要な材料や作り方などの情報を探す必要がありました。
しかし、クックパッドの登場によって、主婦の手から調理前に料理本を開いて、必要な情報を探す作業が不要となり、作りたい料理の名前を打つだけで調理に必要な全ての情報に簡単にアクセスすることが可能となったのです。
曽我製作所が求めていた仕組みはまさに「クックパッド」そのものだったのです。
検索画面に品番や加工部材名を入力するだけで、必要な材料や加工方法が簡単に検索、閲覧できることができれば、作業の理解度のバラつきに関わらず、均一な作業が可能となり、作業前に情報を探す作業が不要になることを確信したのです。
クックパッドから着想を得た曽我製作所では「新人作業員の習熟度のバラつきと情報を探す無駄」を解消するために製造業版クックパッドの実現に着手したのです。
埃を被る結果に終わった第1弾デジタル改革
曽我製作所のデジタル化は決して順風満風なデジタル化ではなく、改革の過程でデジタル化を諦めてしまうほどの大きな失敗に直面しています。
中小製造業企業の現場には、まだまだアナログな業務体系が多く、アナログ業務を続けてきたが故に、ITツールやシステムが苦手と感じるデジタルアレルギーを持った人の割合が多い業界でもあります。
曽我製作所もその1つであり、過去にデジタル化の第1弾としてデータ活用を目的として、現場にパソコンを導入しましたが、広い作業現場に1つしかパソコンが設置されていないため、作業員の方は作業場からわざわざパソコンの設置場所に移動して作業をしなければならない状況となりました。
また、「作業の合間に移動するのが面倒」「順番待ちをするのが無駄」「そもそも使い方がわからない」などの意見から作業員は徐々に敬遠してしまい、最終的に設置したパソコンは誰にも利用されず、埃を被る存在となってしまい、曽我製作所のデジタル化の第1弾は失敗に終わる結果となったのです。
多くの企業はデジタル化失敗という結果から「自社では実現できない」「ITに精通した人材なしでは成し遂げられない」と挑戦を諦めてしまうきっかけとなりがちです。
しかし、曽我製作所はデジタル化の失敗を諦めるきっかけとはせず、次の挑戦の糧とする道を選び、過去の失敗から「作業者の負担にならない、順番待ちをしない、誰でもできる簡単な操作」をテーマに第2弾デジタル化を再スタートさせたのです。
業界からの厳しい逆風
失敗を糧にして始まった第2弾デジタル化を待ち受けていたのは業界からの厳しい逆風でした。
第1弾からの失敗から、デジタル化を成功させるためには現場との二人三脚の改革が必要と考え、作業員1人1人にタブレットを支給し、デジタル化の推進者である曽我専務自ら、業務の合間を縫って丁寧に細かくレクチャーし、ITツールを使うメリットを伝え続け、デジタル化の土台を築く取り組みを行いました。
時間は要しましたが、少しずつ現場の理解を獲得したことで、社内に現場との二人三脚の改革のための土台を築くことに成功しましたが、一方で古い業界からの厳しい逆風を受けることとなります。
予算も知識もない中でアイディア実現に向けて邁進する中で同業他社からは「町工場がタブレットなんか買ってどうする」「町工場にデジタル化は無理だ」「余計なことをせずに金属を切ってればいいんだよ」など厳しい言葉が耳に入ったのです。
当時の業界内ではiPadを製造現場に導入しては活用できずに失敗していく流れが出来上がっていたので、曽我製作所も同じように失敗するだろうと冷ややかな視線や同業他社の言葉が現場に入ることもあり、「今まで通りのやり方でもいいんじゃないか」「既に出来上がっている仕組みを変えなくても」という声が現場から出てきてしまう事態にも陥りました。
しかし、曽我専務が構築した社内の二人三脚のデジタル化の土台は強固なものであり「成功しない、変えられないと言われても、俺たちは変える」と全社が一致団結して取り組みを進めたため、猛烈なスピードでデジタル改革が進んでいきました。
現場と二人三脚で試行錯誤の繰り返し
第2弾のデジタル化において第1弾のデジタル化と最も大きく異なったのは現場社員からの前向きな意見と推進者に任せるのではなく、一緒になって試行錯誤する姿勢でした。
曽我製作所のデジタル化の進め方は以下の通りです。
- 曽我専務がデジタル作業要領書の原案を作成する
- 現場に公開し、意見を求める
- 集まった意見を取り入れる
上記の3つのサイクルを繰り返すことで、現場が本当に求めるアプリの形を構築していきました。
第1弾のデジタル化では現場から意見が出ることは少なく、与えられたものを使うという形でしたが、第2弾では、原案に対して現場から「他の写真を載せた方がわかりやすい」「この情報をコメントで載せたい」などの沢山の意見が飛び出しました。
曽我専務がデジタル化を通して、改めて実感したのは「現場の意見を聞く」ことの大切さでした。

レシピに入れるコメントの文字数は長い方が良いと考えてしまいがちですが、曽我製作所の現場では「長文だと読まないんじゃないか」「読まないとミスに繋がる」という意見から「誰が見ても理解しやすいシンプルなコメント」にするなど、現場の意見がヒントになった機能が実装されています。
デジタル化の推進者である曽我専務は「現場の声こそがシステムに取り入れるべき要素であり、現場の声こそが本当に現場が使いやすくて、作業の負担にならないシステムを構築するヒントになる」と強く実感したのです。
以前は自分が時間をかけて経験してきた技術を公開する事を敬遠していたベテランの職人からも「この加工はこの部分を注意すべきだ」「この角度から見ると作業が楽になる」などのベテランしか知り得ない意見を積極的に出す姿が見られ、まさに「全社員が取り組む理想のデジタル化の姿」が実現したのです。
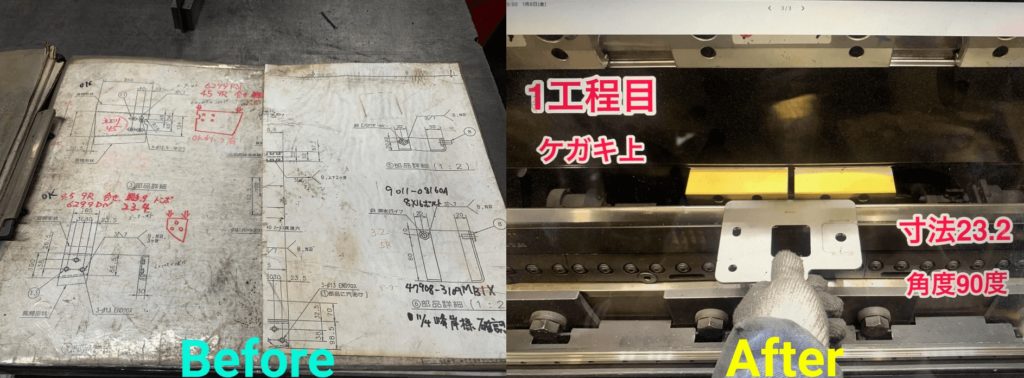
現場の意見が豊富に反映されて完成した製造業版クックパッドは曽我製作所の現場作業に大きな効率化をもたらしました。
新人からベテランまで全ての作業員がiPadを活用して、レシピ検索を行うことで、作業前の情報を探す時間と手間がなくなり、必要な情報に瞬時にアクセス可能となり、習熟度のバラつきに関しても、製品を作るために必要な情報がレシピに網羅されているため、誰がやっても、均一な加工スピードと品質担保が可能となり、作業の標準化にも成功したのです。
デジタル化成功の秘訣とは?
曽我製作所のデジタル化が成功した秘訣はデジタル化推進担当と現場が二人三脚で取り組んだ点にあります。
製造業において多くの企業がデジタル化に取り組んでいますが、その多くがデジタル化に失敗しています。
失敗理由は複数ありますが、その中で特に多いのが「現場を巻き込まなかったがために失敗する」です。
経営層や一部の部署だけで、デジタル化を進めてしまうと、デジタル化の影響で業務が変わる現場から賛同を得ることができず、経営層やアイディアを出した部署の1人相撲となり、デジタル化は失敗となります。
仮に潤沢なIT予算を持ち、ITリテラシーの高い人材が社内にいたとしても、改革推進部署と改革対象部署が二人三脚で進めていく体制が存在しなければ、デジタル化が成功させることは困難です。
曽我製作所におけるデジタル化第1弾も「現場を巻き込まなかった」ために、現場が求めるものと異なる改革になり、パソコンが埃をかぶる結果となりましたが、失敗を教訓に、経営層と現場が共有認識を持って、お互いに意見を出し合いながら二人三脚のデジタル化を進めたことで、曽我製作所は製造業版クックパッドを確立し、現場のデジタル化に成功したのです。
今回の曽我製作所の現場を巻き込んだ二人三脚のデジタル化は「カネなし、ヒトなし、ナレッジなし」の中小企業の理想のモデルケースとなることでしょう。
まとめ
現場との二人三脚で構築した製造業版クックバッドによってデジタル化に成功した後は現場に目に見える大きな変化が現れました。
- 完全週休2日制の実現
- 新入社員が3ヶ月で作業を習得可能に
- 習熟度に関わらない、均一の加工品質
- 加工速度向上による、原価低減
- 作業前の確認作業時間が10分の1に
「エンジニアなし、経験なし、知識なし」の無い物尽くしから始まった曽我製作所のデジタル化は、現場との二人三脚で自社に最適な形のデジタル化を成し遂げることに成功しています。
曽我製作所におけるデジタル化成功の秘訣は「既に世の中にあるシステムをそのまま導入する」ことをせず、「自分たちの業務に対して必要な仕組みを試行錯誤しながら見つけ出した」点にあります。
中小企業では予算不足や人不足を原因にデジタル化を諦めてしまいがちですが、デジタル化は予算がなくても、エンジニアがいなくても実現できます。
曽我製作所は製造業版クックパッドの開発以降もデジタル化に積極的で、社員のタスク管理や全社の情報共有に関するデジタル化にも取り組んでいますので、興味のある方はこちらからご覧ください。
今後は社内に蓄積されたデジタル化のナレッジを結集し「中小金属板金加工企業向けの生産管理アプリ」開発を計画されており、機能紹介や開発状況はインスタグラムを通じて発信をされるそうです。
中小製造業で「デジタル化を実現したいがやり方がわからない」「何から手をつければ良いかわからない」とお悩みの方は是非、曽我製作所のインスタグラムをチェックしてみるはいかがでしょうか。
Anytiveでは中小企業のデジタル化を支援するアプリ開発やECサイト制作を行なっています。
「アナログ業務をデジタル化したい」「少ない予算でデジタル化を実現したい」という場合は、お力になれると思いますので、是非お声がけください。