モノづくりにおいて金型は質の良い製品の大量生産に欠かせないものであり、日常のメンテナンスや修理管理などの保全活動が品質を左右する重要資産ですが、メーカーの金型管理があまりにも残念でロクな管理をしていません。
お金もない、管理する人もいない中小企業なら金型管理が疎かになるのは100歩譲って許容しますが、何百人もいて金型保全部もあるような、大手メーカーが「Excel」や「紙の台帳」で形骸化した管理をしているのです。
大手メーカーが「台帳を使って管理している」と声高々に言いますが、実際は形骸化しており、誰も中身を知らない、金型は外部の業者任せのお粗末すぎる管理なのに「管理できてる」と言うのは残念すぎます。
管理しているは愚か、故障やトラブルを予知することをせず何か起きてからようやく動く保全部、外注に丸投げしてるから何も詳細はわからないような管理台帳に何の意味もありません。
この記事では日本の大手メーカーで起きている残念すぎる金型管理の内容を解説すると共に未だにExcelや紙の管理台帳を使っている保全部に最適な管理ができる製造業のためだけの金型アプリを紹介します。
大手メーカーですらExcelでお粗末な金型管理
お金も人もノウハウもある大手メーカーなのにお粗末すぎる金型管理をしている会社が多すぎます。
金型屋がどんどん廃業したことで焦り出して、金型管理を見直す大手メーカーが増えていますが、金型は生まれてから死ぬまでの時系列の変化を管理し、すぐに閲覧できて初めて、管理していると言えます。
が、実態は名だたる大手メーカーすら、「Excel管理台帳」「紙の管理台帳」といつの時代の話をしてんのかレベルのお粗末管理です。
ここでは実際にお粗末すぎる金型管理に関して解説します。
何の意味もないExcel管理
もう悲しくなるのですが、令和の時代、DX、デジタル化が叫ばれている中で未だに「Excel管理」が基本であり、ただ台帳のように羅列で書かれた情報だけで管理できていると自慢げでいるメーカーが多すぎます。
Excel管理をしているメーカーが心で思っていることを代弁します。
- 一覧にはなっているけど、過去のメンテ履歴や修復履歴が紐づいていない
- 金型の生まれたから現在までの歴史は毎回、調べ尽くすので時間を浪費
- 部署にいる熟練の人間しかファイルを扱えない
- 簡単に過去の履歴を調べ上げることができない
- 外注とのやりとりはメールなので情報が台帳にない
情報をすぐに取り出せて、経験問わずに誰でも情報を扱えて初めて管理できていると言うのに、「すぐにデータが見つからない」「ベテランしかできない」「情報が分散している」のが大手メーカーの実態です。
Excelは確かになんでもできて便利なツールですが、所詮はExcelであり、器用貧乏である手段と理解し、本当に金型管理しようと思う人はまずExcelなんて使いませんし、専用のツールできちんと管理します。
要は金型管理を適当にやっている会社は金もかからないし、管理できているように見えるExcel管理、金型の重要性を理解し、しっかり管理しているメーカーはお金をかけて専用ツールで管理しているのです。
そもそも欲しい情報を1日中、時間をかけて頑張って探さないと情報を手にできないようでは金型保全活動がそれだけ遅れてラインが止まることの大問題を理解していないことが悲しいですよね。
情報が分断された金型管理でも満足らしい
メーカーは予防保全に極めて重要な「トラブルの原因と対策の時系列が追えない」Excelや紙の管理台帳で満足しているのです。
金型を使うのは現場、金型のトラブルやメンテ手配するのは保全部、実際に金型を手を加えるのは外部の協力会社で、保全部は現場からのトラブル報告、協力会社の金型屋からの作業報告はどうやって管理してるんですかね。
結論は「管理しているようで全く管理してない」が答えで、Excelで管理しているのはあくまでも金型の情報だけで現場からのトラブル報告は紙、協力会社の金型屋からの報告はメールで情報が分断されているのです。
保全部は金型に何か起きた際はトラブルの原因を理解したいはずですが、実情は「事後報告」が基本で現場にめんどくさい紙で書かせて報告をさせる企業が多いですが、これも形骸化していた「現場が報告書を書いてくれない」のです。
仮に現場がきちんと紙に書いてくれたとして、紙だから管理台帳に「転記作業」が必要ですが、この令和の時代に紙でやるのがどれだけ時代錯誤なことをしているかという話です。
そもそも現場が事後報告する点も大問題であり、原因がわかっているのに「現場がめんどくさがって書いてくれない」で思考停止で終わらせているのが残念であり、「現場が報告しやすい仕組み」にすれば良いだけでは。
また、修理や工事を依頼する協力会社からの作業報告はメールでやり取りする保全部が多いようですが、これも管理台帳に紐づいてないから、わざわざ全部転記している会社もあれば、メールで残すだけの恐ろしい会社もあります。
何かあったときにメールを検索して、該当するやり取りを見つけるのが無駄だと気づかないのですかね。
そもそも管理台帳というのは「必要な情報」「関係各位とのやりとり」が全て記録され、簡単に取り出せて初めて目的を果たすのに、原因報告は紙、対応対策はメールなんて形骸化しているとしか言えませんよ。
形骸化に気づいても見ないふり
大手メーカーの保全部の方は「この金型管理、意味なくない?」「昔からのやり方を続けているだけだよね?」と多分気づいているけど、誰もおかしいと言わないから機能せず形骸化した金型管理台帳を見ないふりしているのです。
本当に人間というものは変化が怖い、できれば変わりたくない「やらなくていい方向に逃げる生き物」ですが、メーカーのずっと意味なく続ける金型管理は変化することを避けたせいで形骸化した負の産物です。
毎日のように金型管理のExcelシートを開いて、情報を探して、見つからなくて、現場から急かされてイライラするを繰り返しているのに「この金型管理、機能してないよね」と言わないのが不思議でしょうがないです。
金型管理台帳の目的は「金型に何か起きた際にすぐに情報を拾い出して、保全活動を行う」ことなのに、「必要な情報が取り出せず、永遠とExcelシートと睨めっこ」している時点で「形骸化している」と声をあげるべきでは。
そもそもメーカーさんにとって金型は重要な技術資産であり、技術的優位性を保つ道具であるのに適当に管理していることに誰も声をあげない、やばいと思っても言わない環境が本当に恐ろしいです。
もしも主力製品を生産する金型にトラブルが起き、大至急で金型を元に戻さないといけないのに、欲しい情報が見つけられず、対応も遅れて、生産を止めてしまったら大損失になるという危機感はないのでしょうか。
多分、形骸化しても何も行動しないのは「協力会社の金型屋がなんとかしてくれるから」で、どうしようもなくても「金型屋さんが対応してくれる」と依存しているから「なんとかなる」と現状維持を貫くのです。
でも、「何とかしてくれた金型屋」がどんどん廃業して、「自分たちが金型をなんとかしないといけない」ことになったら形骸化した管理をしてたら、もう終わりですよね。
「何か起きない」と動かない保全部
「何か起きる前に事前に対策を講じて最小限の被害に抑える」のが金型保全部のミッションであるのに、多くのメーカーでは金型保全部は「何かあって初めて動く」「あ、問題だ!よっこらしょ」と完全に待ち体質の部署です。
設備保全の目的は、設備が異常で停止したり、壊れないように対策をすること、仮に生産が停止したとしてもその停止時間を最小限とする活動、より長く設備が稼働できるようにすると定義されてます。
が、「実態は壊れないように対策でなく、壊れたら動こう」「機械が止まっているのに情報を探すだけで時間を食って停止時間がどんどん長く」なるで目的を果たしていないように見えます。
ここでは「何か起きない」と保全部の実態を解説します。
金型が壊れるのを待つ部署に
現状の形骸化した金型管理に危機感を持っている方が言う言葉が「我々は壊れるまで決して動かない保全部」「まるで壊れるのを待っているかの壊れ待ち部署」であり、壊れるまで何もしない待ちの部署なのです。
金型保全の理想として挙げられるのは「保全部としてメンテナンス時期が来たら、壊れる前に対策を講じる部署に」「壊れる前に管理システムで予防保全に動ける仕組み」を有することですが、悲しいかな理想で終わっています。
保全部の実態は「仕事のきっかけは金型が壊れる」ことであり、壊れるまでは何もせずに、腰を落ち着かせて待っている、ただ待つであり、現場から壊れたの連絡が来ると「よっこいせ、やりますか」と重い腰を上げるのです。
保全部という名が名が泣く様な仕事の仕方ですが、形骸化した管理と業務をしていることに気づいていないのか、見て見ぬ振りをしているのか大手に分類されるメーカーですらこんな仕事の仕方をしています。
おそらくですが、上層部から金型保全部は注目をされないから問題が問題と捉えられぬまま、時間が過ぎているのであり、経営会議で売上やコストのように金型保全に関する数字報告はないから、経営者や役員が気づかないのです。
絶対に経営者や役員が「壊れたから動く、壊れるまで何もしない保全部の実態」を知ったら間違いなく大激怒するでしょうが、実態として経営報告に上がりにくい部署だから形骸化した管理を続けても何の問題もないでしょう。
でもね、最近になって急に金型管理を見直す大手メーカーさんが急増しており、その背景は「なんとかしてくれてた金型屋が廃業した」せいで、自分たちでなんとかしないとヤバくなったからです。
情報が分断されているせいで動けない
保全部の中には「壊れる前に何かしよう」と努力をしている方もいるかと思いますが、現実は「壊れるまで何もできなかった」であり、この原因は「情報が分散されていて、必要な情報がすぐに取れない」ことです。
保全部が金型が壊れる前に動こうとする場合には以下の情報が必要になるはずです。
- 前回壊れた際のショット数
- 過去に起こったトラブル履歴&修復履歴
- 類似する金型でよく起こるトラブル
- 外注からの金型診断やフィードバック情報
これらが金型データに紐づいていれば、すぐに壊れそうなデータを持つ金型をピックアップして生産計画の前に保全活動をするという本来の目的を果たせるのですが、「データがいろんなところに分散して見つけられずにいる」のです。
要は保全活動に必要な情報をすぐに見つけられないせいで、何か起きる前に動けないという状況であり、諸悪の根源はExcelで管理して、付随する情報がどこにあるかわからない管理体制にあります。
シンプルにいうと、「データ探しを頑張れば壊れる前に動ける」がデータ探しを頑張れない、調べるのに手間がかかり過ぎて他の仕事が終わらなくなるから、できないという形です。
形骸化したExcel管理に固執するから、本来の壊れる前に動くができずにいることを理解していない保全部が多過ぎます。
ですが裏を返せば、壊れる前に動くためには金型情報にショット数や過去のトラブル&修理履歴、金型会社からのフィードバックが紐づいているシンプルな管理ができる仕組みがあれば良いだけなのです。
きちんと金型を管理したいなら、Excel管理を辞めれば良いだけで予算がある大手メーカーならすぐにできることなのに誰もしないのが不思議でなりません。
金型屋の廃業で焦り出す保全部
大手メーカーが協力会社である金型屋の相次ぐ廃業で焦り出しています。
新型コロナをきっかけに令和になって次々に団塊の世代の経営者が高齢化し、当然ですが、後継者もいないため金型屋がどんどん廃業しており、メーカーの頼みの綱であった「なんとかしてくれる金型屋」が消えているのです。
今までの形骸化した金型管理をしていても、情報が不足していても、金型を持っていけば、技術と金型屋の社長の頭の中の勘ピュータでなんとかして金型を戻してくれたが、今後はもう「形骸化した管理」では通用しなくなります。
- 今まで:金型がダメになりました。いつものように直してください
- 金型屋:わかった!頭に仕様があるからいつもの形で対応する
上記のようにデータや過去の履歴を出さなくても、長年の経験と取引の中で培ったやり取りでなんとかしてくれていましたが、これからは以下のような「必要なデータを出さないと対応できない」世界になるのです。
- これから:金型がダメになりました。直してください
- 新たな金型屋:過去の情報やデータをいただけないと対応できません
当然ですが、新たに見つけた金型屋には廃業した金型屋に存在したノウハウや経験、金型への理解、過去の経緯も知らないので情報やデータなしで対応するのは金型を壊すリスクなので誰も触りたがりません。
形骸化した金型管理をするメーカーは大ピンチですよね、今までのように「丸投げで任せた」という必殺技が使えずに壊れた金型を直すためには日頃から管理している金型管理台帳の情報を出さないといけないのです。
きちんと運用されている金型管理をしているメーカーはなんてことはありませんが、形骸化した金型管理をしているメーカーは金型が壊れたら総動員でExcelから必要なデータを頑張って手間をかけて探さないといけません。
めんどくさくて手間がかかったとしてもデータを見つけないと金型が修理できないのでやるしかないですよね、残業して他の仕事を後回しにしてでもやるしかありません。
だってもしも金型が直せなかったら、現場に怒られるし、経営層にも今まで形骸化した金型管理をしていたのが報告されてしまい、「壊れてから動く保全部の実態」がバレてしまうから。
金型管理を見直したいメーカーに最適な金型アプリ
この記事を読んで、自社のExcelや紙の金型管理台帳が形骸化していると危機感を持った方はぜひここで紹介するメーカーに最適な金型管理アプリの活用を検討ください。
大手メーカーさんであれば担当者レベルで決済できる利用料なので、試しに見直してで使ってみるのミニマムスタートで形骸化した金型管理を見直すことができるチャンスです。
シンプルで管理しやすい
Anytiveの提供する月額3万円で使い放題の金型管理アプリはPC・タブレット・スマホでシンプルに金型管理が実現できる機能を備えたオールインワンアプリです。
図面PDFから各種写真画像まで全て格納できるため、1データに金型にまつわるすべてのデータを保管運用する仕組みなのでもうExcelのように関連する情報を探す手間はありません、全部紐づいているから。
登録した金型データはQRコードを生成して、金型に貼り付けてスマホでスキャンすれば、すぐに金型情報に飛べるので、気になる金型があれば、現場もスマホをかざすだけでOKなのでわざわざ金型を調べてデータを探すも不要です。
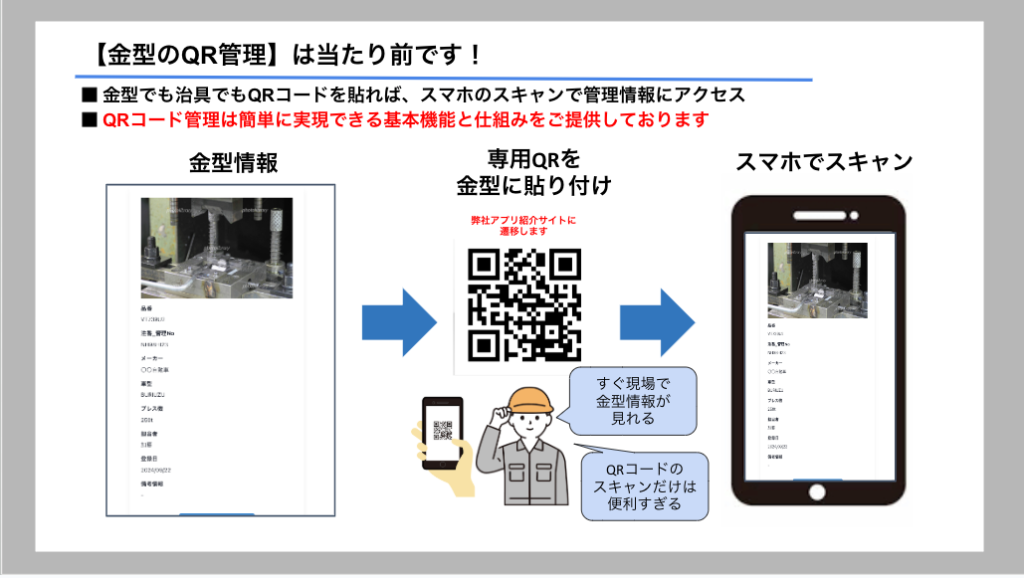
世の中にはQRコード運用をするために何十万も費用がかかるシステムが存在しますが、あれは完全にぼったくりでありQRコード生成なんて無料でできる仕組みなので無駄なお金を保全部の方が出す必要はありません。

また、保全部が1番早く詳細まで知りたい現場からのトラブル報告ですが、金型アプリには現場からの報告機能も用意しているので、現場からの報告に関しても紙を卒業し、デジタル化が実現できます。
- トラブルが起きたら金型のQRを読み込み
- トラブル報告から報告内容を音声入力
- 申請をするだけで保全部にすぐに連絡完了
金型アプリは現場にとことん配慮したアプリであり、軍手をわざわざ外さなくても、スマホでの音声入力に対応しており高精度のAIが音声を識別し、自動で入力をしてくれるので現場も嬉しい限りではないでしょうか。
金型が生まれたからの変化を全て追跡
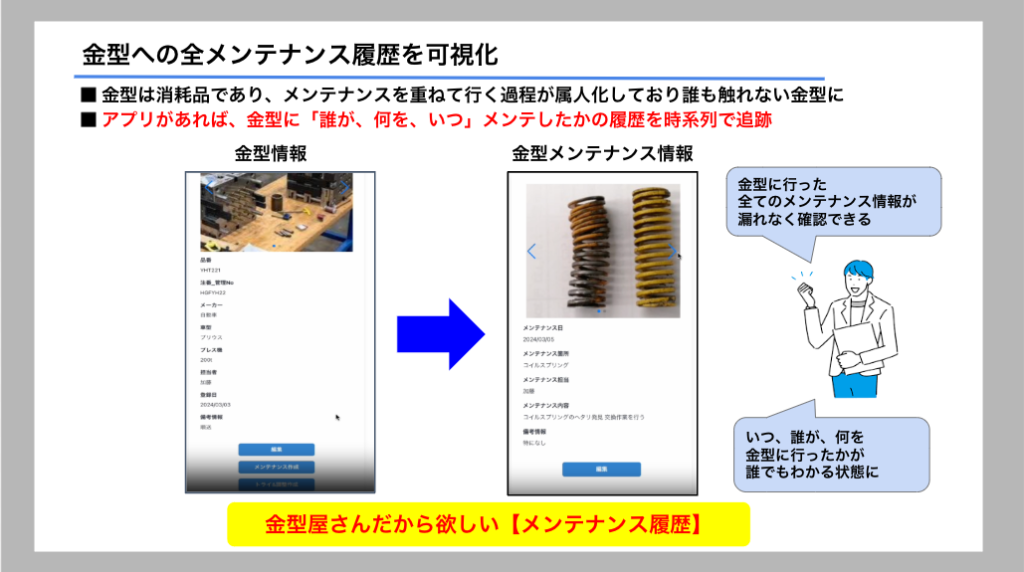
金型管理アプリは保全部が時系列で管理した「メンテナンス履歴」と「改造&トライ履歴」の両方を金型データに紐付けて管理することが可能なため、金型が生まれてから現在に至るまでの全てを追跡可能です。
保全部が知りたい、そして協力会社の金型屋から求められるのはこれまでに金型がどのような手を加えられたのか、そしてどの部分が故障履歴があるのかという点ですが、Excelではこの関連データを一緒に管理ができません。
しかし、金型アプリは金型データの子供として「メンテナンス履歴」と「改造&トライ履歴」を保存できるので金型データを見れば、関連する情報を全て紐づけて閲覧できます。
極めてシンプルな管理方法で、「いつ、誰が、何を、どうやってメンテしたか」を画像付きで保存する仕組みですが、金型データにメンテ履歴が紐づいているだけで以下のようなメリットを保全部と協力会社の金型屋は受けられます。
- 金型データを呼び出せばすぐに過去の経緯がわかる
- アプリを見せながら協力会社に過去の経緯を説明できる
- 協力会社のメンテ作業内容を記入してもらえば転記がなくなる
ただデータを紐づけるだけで部署内で調べるだけでなく、外部の協力会社にもすぐに情報を共有することができるので、金型のメンテ作業までの時間を短縮可能になります。
同様に金型アプリでは「改造&トライ履歴」を残す機能も有しているので、今までは外部の協力会社から受けていたメールや紙での作業報告もアプリ内に紐づけて残すことが可能になります。
- 外部の金型会社が作業内容+結果をアプリに入力
- 保全部はアプリを見れば結果がわかるので、転記不要
- 次回何かあった際もアプリを見れば過去の作業内容がわかる
メーカーの形骸化した金型管理の問題点は「金型に関するデータややりとりが分断されていること」で「探す手間」「調べる手間」が生まれるのが問題ですが、全部繋がっているアプリがあれば万事解決ですよね。
データ活用で金型保全部の価値が変わる
金型アプリはただデータを管理するだけではなく、蓄積したデータを予防保全と金型設計時の壊れにくい金型設計のための保全部からの提案エビデンスデータになります。
保全部の理想は「何かが起きる前に動いて、未然に防ぐ」ことであり、未然に防ぐためには過去どの程度のショット数で故障してメンテをしたかのショット管理が必要です。
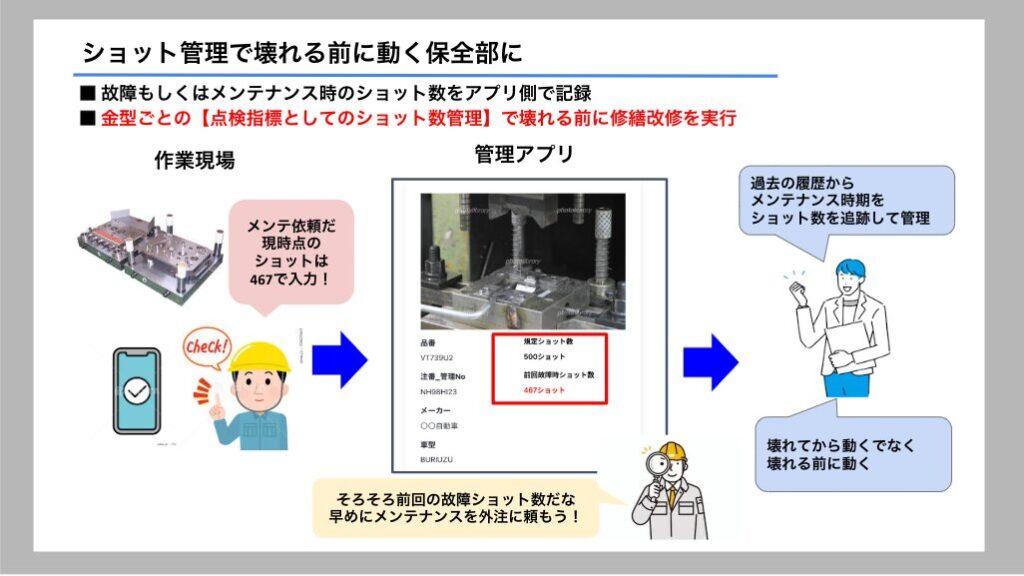
金型アプリは現場からのメンテ申請の際にショット数のログを残す仕組みを提供しており、毎回メンテナンスを実施する際にその時点のショット数を追跡することができます。
ショット管理から過去の傾向で故障タイミングやメンテタイミングを明示的な記録データから読み取り、現場から連絡が入る前に、「データからそろそろ保全活動しよう」というデータ活用による事前予防作業が可能になります。
理想の姿として捉えていた「何か起きる前に対策をする」ために必要な方法はシンプルであり、やろうと思えばどのメーカーも簡単に理想の保全活動が実現できるのです。
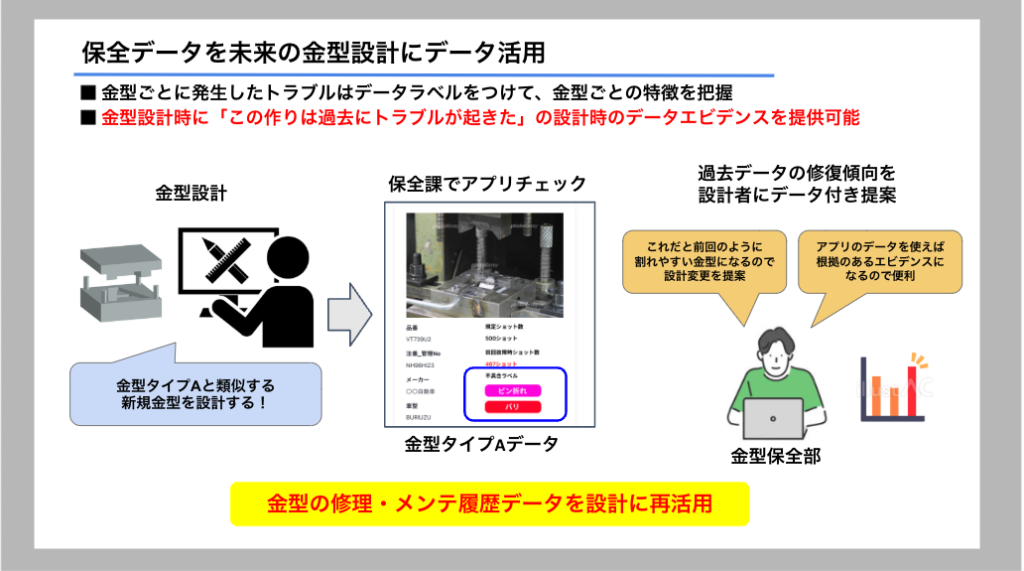
そして保全部は事前予測の保全活動にのみならず、設計部が新たな金型を起こす際に過去に故障した履歴データやメンテナンス情報を活用して、「壊れにくい金型設計」に役立つ情報をエビデンスとして提示が可能になります。
言うなれば、「保全データを活用した未来の金型設計」であり、過去に製造した金型と類似する金型を作るケースが多いため、金型でよく起こるトラブルをデータとして提示すると「壊れにくい金型設計」が可能になります。
類似する金型の修理履歴データを吐き出して、過去に何度もピン折れが発生しているのであれば、段付きのピン構造を提案するなど、普段から金型の保全活動をしている人間だからできる提案がデータを基に実現できるのです。
設計部もただの思いつきでなく、実際の金型の修復データをエビデンスとして挙げられると、「これはいいデータだ」「根拠もあるし設計変えよう」と納得して提案を飲んでくれます。
要は金型保全部はただ金型管理するのでなく、保全活動で溜まったノウハウを金型設計に反映することで、社内でより価値のある部署へと変貌する、現場からのノウハウを設計に役立たせるボトムアップのモノづくりが完成します。
まとめ:メーカーはExcelと紙の金型管理から脱却せよ
この記事では大手メーカーで起きている残念すぎる形骸化した金型管理を解説すると共に未だにExcelや紙の管理台帳を使っている保全部に最適な管理ができる製造業のためだけの金型アプリを紹介してきました。
はっきりと言いますが、令和の時代に「Excel」や「紙」で金型管理をしているメーカーは時代遅れであり、保全部も社内で価値の低い立場になってしまいます。
これからの時代は金型業者も更に廃業数が増えていくので、メーカーは社内で適切な金型管理ができていないと誰も手が出せない、中身を知らない「野良金型」の世話をする羽目になるでしょう。
時代遅れの保全部から「何かが起きる前に事前に動く」「データ活用で設計にまで提案」ができる保全部に変貌する方法は簡単で適切な管理の仕組みを使えばいいだけで、弊社の金型アプリは製造業にとって最良の選択肢です。
弊社は製造業のメーカーが下請法に抵触しない金型管理に特化した仕組みである「AnyMold」を提供し、メーカーの形骸化したExcelでの金型管理を解決する支援をしております。
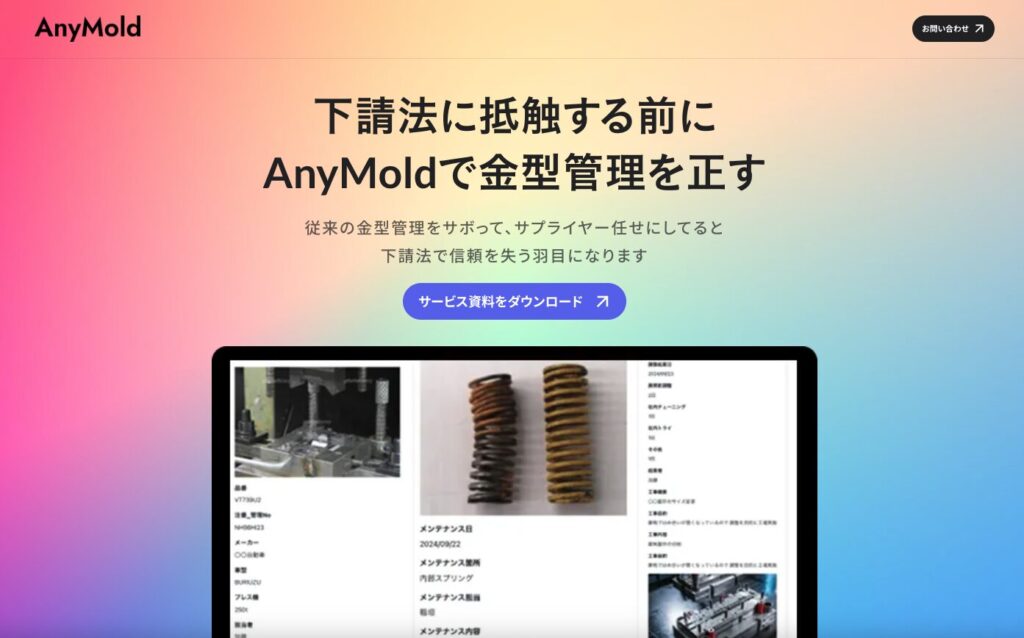
「デジタル化したいけど何から始めるべきかわからない」「なるべき低コストでデジタル化したい」「最適な仕組みを丸投げで実現してほしい」などのお悩みを抱える町工場様はぜひ資料請求にてサービス内容をご確認ください。
