金型屋の倒産が止まらず、このままメーカーは指を咥えているといずれ、自社の懇意にしている金型屋の廃業も時間の問題であり、自社金型を移管ができない絶望的な状況が待ち受けています。
大手自動車部品金型メーカーのエム・ビー・シーの自己破産手続き、自動車から航空機まで金型性を鵜を行っていた三恵金型工業の事業停止など零細ではなく規模の大きい金型会社が次々と廃業をしています。
今は「連絡すれば元通りに直してくれる金型屋」がいるかもしれませんが、金型屋の大半は家族経営でかつ全員社長が高齢者で、後継もいない、いつまで仕事ができるかわからない綱渡り状態です。
にも関わらず、メーカーの保全部は金型管理がお粗末で全て金型屋の社長におんぶに抱っこ状態で何の管理もしていない状態なので、もしも懇意にしている金型屋が廃業したら、「金型移管ができない状態」に陥ります。
この記事では金型屋の倒産を指を咥えてるメーカーは、いずれ誰も自社の金型の面倒を見てくれず、移管しようにも移管するために必要な情報がないので、誰も相手にしてくれない状態になる点を解説します。
日本の金型屋は絶滅危惧種
日本において金型加工を行う町工場はもう絶滅危惧種と言っていいほど、工場の数を減らしており、生存する工場も大半が団塊の世代の社長が老体に鞭を打って頑張っている状態ですが、いつまで続けられるかの状態のはずです。
町工場という括りの製造業の工場はコロナによって生まれた「需要減少」をきっかけにどんどん数を減らしており、都会はまだギリギリ、地方は探しても町工場がない状態の危機的状況ですが、特に金型に関しては絶望的です。
ここでは日本のおける金型屋の状況と潜んでいるリスクに関して解説します。
金型屋の減少が止まらない
日本全国でもう金型屋は4000社しか存在しない、47都道府県で考えると1つの件にもはや100社も存在しないほど数が減っている現実をご存知ですか?
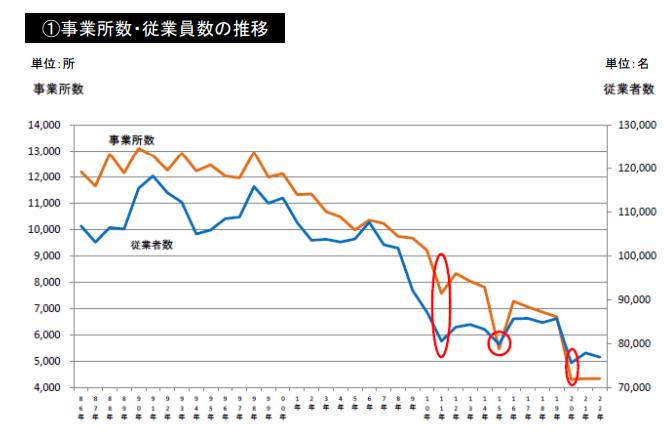
日本金型工業会が算出している事業所統計データですが、1986年には12000社ほどの金型会社が存在しましたが、最新の2022年時点では事業所の数は4000社で約3分の1まで減っているのです。
全国47都道府県ある中で4000社しかないのは県内に100社も金型が存在しないくらいまで金型屋は減ってしまっているのであり、これはもはや絶滅危惧種としか言いようがありません。
金型屋の数が一気に減少した原因は2020年の新型コロナウィルスの発生で1年で3000社近くの金型屋が廃業しており、まさに2020年が金型屋の転換期、「家族経営で細々とやっていた町工場の淘汰」が起きています。
これだけの金型の廃業が起きているということはメーカーが考えるべきは「自社の保有する金型をこの先も保全し続けられるか」という危機感です。
今までは懇意にしていた金型屋があり、長年の取引背景と金型屋の社長が全部知っていたから「丸投げしてOK」でしたが、頼みの綱の懇意の金型屋が廃業したら、どこか他の金型屋に移管しなければなりません。
が、これだけ金型屋が減少をしていたら、工場の近くの立地のいいところに金型屋はまず存在せず、金型屋があったとしても「他のメーカーで一杯」と断られる、まさにどこにも移管できない未来は十分にあり得るということです。
父ちゃん母ちゃんで後継者なしの金型屋
「金型屋の心配をしてない保全部は愚か者」であり、その背景は金型屋の大半が9人以下の家族経営、父ちゃん母ちゃんの工場であり、後継者もいない、そしてデータ管理の仕組みもない、勘に頼った環境だからです。
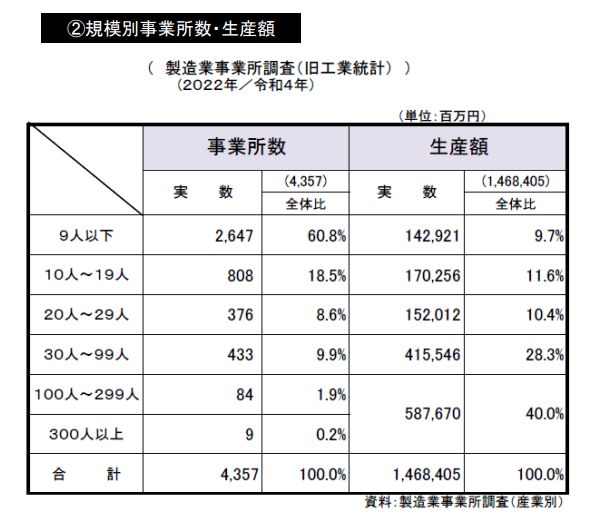
日本金型工業会が算出する事業所の規模別統計データを見ると、4357社ある町工場のうち、6割以上が9人以下の事業所であり、いわば「父ちゃん母ちゃんの家族経営の町工場」なのです。
メーカーは安い、早い、無理を言えるから「父ちゃん母ちゃんの町工場」が大好きですよね、値上げもしてこないし、いつまでも安い値段で仕入れられる甘い汁を啜っていると思いますが、裏側にあるリスクわかってますか?
- いつまで事業を続けられるか誰もわからない
- 後継者が基本的に存在しない
- データ管理なんて存在しません
父ちゃん母ちゃんの金型屋が会社を畳む時は「体が限界を迎えた時」「何か病気になった時」であり、計画性はなく突発的にいきなり電話で「もう限界です」と保全部に電話が来てある日、依頼できなくなる恐ろしい爆弾です。
そして金型屋を継ぎたがる若者は滅多に存在せず、父ちゃん母ちゃんの金型屋は漏れなく後継者不足であり、会社を存続させるために必要な後継者の育成はしていないので、今の社長がダメになったらもう、会社は存続できません。
そして1番のリスクが父ちゃん母ちゃんの金型屋には「データ管理」なんて概念は存在せず、過去の作業内容や金型の詳細情報は全て社長の頭の中でメーカーも自社の金型の情報を手にするのが不可能な危険極まりない状態です。
1番考えられるわかりやすい絶望のシナリオは以下の通りです。
- 懇意にしていた金型屋の社長が病気になり、入院などの離脱
- 任せていた金型が全て宙ぶらりんに
- 金型に関する情報が社長の頭の中で保全部もわからない
- 移管しようにも金型情報を出せないので誰も引き受けてくれない
- 野良金型が生まれ、誰も面倒を見れない
大手メーカーの保全部でも金型管理が形骸化して、社内に何も情報がないようなお粗末管理を平気でしている状態ですが、それが成り立つのは懇意にしている金型屋がある内であることに危機感を持つべきなのです。
以下の記事では大手メーカーでも平然と行われている残念すぎる金型管理の実態とその原因がExcelによる形骸化した管理である点を解説します。
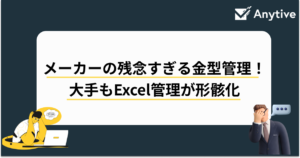
金型屋の囲い込みは始まっている
製造業のメーカーの動きは2極化しており、大半は「今まで通り懇意の金型屋におんぶに抱っこで何もしない」の保守派で、一方は「いずれ廃業する金型屋に変わる新たな金型屋の囲い込み」に動く行動派です。
特に大手のしっかりと未来を見据えて行動をする保全部があるメーカーは県内、県外問わずで自社の金型の保全協力をしてくれる新たな外注先探しを始めています。
その背景として既に動いているメーカーは「やばくなってから動いても遅い」という危機感が強く、いち早く金型屋を自社で囲いこまないと他社に限りある金型屋を取られてしまうという競合対策の面がとても強く出ています。
「大手が動き出したらすぐに金型屋が刈り尽くされる」と資本力の強いメーカーが金型屋確保に動いたらあっという間にお金を武器に金型屋を引っぺがされるリスクがあるので、早期に囲い込むことで予防線を張るのです。
金型屋の生産能力やリソースは限られており、金型屋がここまで少なくなった以上、誰がそのリソースを使うかという話になり、仮に金型屋を見つけて問い合わせをしても「よそでいっぱい」と断られるのが常になります。
危機感があり、未来を見据えているメーカーの保全部は既に金型屋の青田買いを始めており、指を咥えて何もしない、やばくなってから動こうとしているメーカーの保全部は金型屋を囲い込まれていることにすら気づいていません。
金型屋の供給が少なくなっている中で、メーカーの需要過多になったら当然、値段も上がりますし、そもそも相手にされないような状況は間違いなく訪れますが、この行動の違いでメーカーの未来は決まるのでしょうね。
以下の記事では金型職人の絶滅前にメーカーの保全部は改革に望まないと、誰も金型の面倒を見てくれない状態を避けることができず、生産すらおぼつかないような状況になる未来に関して解説します。
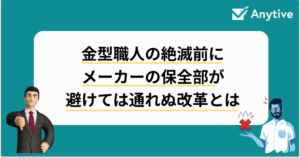
金型管理をサボったツケを支払う
メーカーはもう「電話1本で金型が保全できる環境」のような楽できる環境ではないことに気づいてください、適切な管理を保全部が行い、新規の金型屋が必要とするデータを出せる環境に変革しないと痛い目を見ます。
「壊れたから対応して欲しい」と電話1本で当たり前に保全活動が終わるような環境に甘んじている保全部の方に警鐘です。
いずれ、過去から懇意にしている金型屋は廃業し、「電話1本でなんとかしてくれる味方」はいなくなり、自分たちがしっかりと金型管理をしてデータ管理をしないと保全活動が成り立たなくなります。
ここでは金型管理を適切に行わずにExcelなどで適当に管理しているメーカーの保全部に訪れる「金型管理をサボったツケ」に関して解説します。
メーカーの金型管理は形骸化
多くのメーカーは「金型管理をしている」と自慢げにドヤ顔をしてますが、実態はExcelを騙し騙し使った体制であり、管理とは程遠いただの形骸化した仕組みの上であぐらをかいてます。
本当に驚くべき事実で、日本人なら誰もが知る大手メーカーのグループ会社でも「金型管理システム」は存在せず、管理方法はExcelを管理台帳代わりにしており、中身を見ると何も管理できていないのが普通です。
- そもそもデータが分散化されており、管理できてない
- 金型に関する情報は頑張って探さないといけない
- Excelファイルが多すぎてどのデータが正しいか不明
上記がメーカーで行われている金型管理の実態であり、正しい管理とは必要なデータが「欲しい時に、いつでも、誰でも、簡単に取り出せる」ことですが、メーカーは「欲しいと思ってもすぐに取り出せない、探すから始まる」のです。
「弊社はISO9000取得済み」サプライヤーには「ISOないと取引できません」と上から偉そうに言ってきますが、自分たちの金型管理はISOに適さない形だけのことをやっているのを隠して滑稽でしょうがありません。
もう少しメーカーの形骸化している金型管理に関して掘り下げると、以下のように金型に関する情報が至る所にバラバラに保管されているので、目の前にある金型の情報をすぐに見るのが実質不可能という状態です。
- 金型に関する基本情報はExcelに
- 金型図面はローカルPCのフォルダの中に
- 過去の修理履歴は個人メール文章の中
- 現場からのトラブル報告は紙の報告書で段ボールの中
1つの金型に関連する情報が全て別々の場所に保管されており、必要な時は1つずつ調べて探さないといけない状態を管理できていると言っているのが恐ろしい限りであり、これを管理だと思っているならISOは返上ですね。
Excelは誰でもコピーできて、複製ができる、かつ誰がデータをどのように変更したかの履歴も残らないので、本当に嘘偽りのない正しいデータかという確証もない仕組みなのに管理としてなんとも思わず使っているのも危険です。
なぜ、Excelを使っているのかの答えは単純でどのほかにも口を揃えて、「無料だから」ととんでもない答えが返ってきます。
上記のようにメーカーで行われている金型管理は管理とはいえない体制ですが、どのメーカーもなんの疑問も危機感も持たずに形骸化した形で運用しているのが実態です。
以下の記事では製造業で当たり前のように行われているExcel管理がお粗末の極みであり、実際に行われている恥ずべきデータ管理の実態を解説しますので合わせてご覧ください。
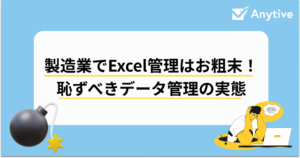
保全部は「何か起きてから動く」の待つ部署
形骸化した金型管理を行うメーカーの保全部は「何か起きたら」重い腰を上げて動くような待ちの部署であり、「何かが起きる前に対策をする」という考えは残念ながら頭に存在しません。
保全部の存在意義って、「金型や設備が壊れたら直す」ではなく「壊れる前に事前に予知して対策する」のはずなのに保全部は現場から壊れたと連絡がなければ何もしません、本当に何も対策をしません。
「前回に壊れたショット数と近いからメンテしよう」「過去の履歴で修理した場所の点検しよう」という行動をするのが普通ですが、「保全部はしない」であり、厳密に言うとデータ管理してないからわからないが答えです。
何も超人的な職人の目線で金型を見るだけで不具合やメンテナンスに気付けと言っているのでなく、「過去から蓄積したデータを活用して保全すればいい」だけなのですが、形骸化してるからデータ活用できないですよね。
- 過去の故障した時点のショット数がどこにあるかわからない
- 時系列で壊れた履歴やメンテナンスした履歴が見えない
- そもそも1個ずつ金型のデータを探して見る時間がありません
上記が何か起きる前に対策をしない保全部の言い分だと思いますが、全部言い訳ですよね?。
事前に察知して行動できないのは正しい仕組みを入れずに形骸化したExcel管理を続けるからデータは蓄積しないし、探さないといけないのがめんどくさくてデータ活用に取り組めないのではないですか。
壊れてから重い腰を上げてしか動けない保全部になんの意味があるのでしょうか、壊れたら動けならバイトでもできますし、社員にやらせて価値が出るような仕事なのでしょうか。
そもそも保全部が形骸化した管理をし続けても何も改善されないのは「経営層にバレてない」からで、経営会議で保全部が議論の中心に上がらないので形骸化したExcel管理をしていることに気づいていないから誰も行動しないのです。
でも、もしもこの先に金型屋の廃業が増え続け、金型移管ができない問題が発生して、経営層に形骸化した金型管理がバレたら大目玉喰らうのは間違いなしであり、これが保全部が今すぐに対策に移るべき理由になります。
金型屋に敬遠される
形骸化したExcel管理を続けた場合に支払うことになるツケの1番重いもの、それは「移管先の金型屋が見つからない」厳密に言うと、金型屋はあるけど敬遠されて、金型を見てもらえない悲劇です。
遅かれ早かれメーカーの保全部は「過去から懇意にしている金型屋を失う事態」は確実にやってくるものであり、代替先となる新たな金型屋に自社金型を移管しなければなりませんが、Excel管理のせいで移管ができなくなるのです。
Excel管理の形骸化した管理をしている保全部が金型屋から言われる言葉は次の通りです。
- 移管対象の金型に関する基本データ、図面、関連するメンテ情報などを出してください
- データがない場合はうちは金型に手が出せないので、受け入れはできません
- 「なんとかお願いします」と言われてもデータなしで金型に何かあったら怖いので無理です。
形骸化した管理をしている保全部は金型屋に上記の断り文句を言われ続けて、どの金型屋も移管を受けてくれない、むしろ敬遠するような状態でどこも金型を見てくれない結末に陥ります。
これは金型屋が殿様商売をしているのではなく、当たり前の対応をしているだけで悪いのは新規の金型屋が作業をするために必要な情報を出せないメーカーの保全部が悪いのです。
当たり前ですよね、だって今まで取引したことがない顧客の金型を扱うのに、事前情報なしに触って、金型を壊したらそれこそ大問題になるので、事前に情報をくださいと言うのは至極真っ当なことに他なりません。
でもメーカーがデータを出せないのは懇意にしていた金型屋は「長年の取引」があったからデータなしでも金型屋の社長がなんとかしてくれていた、ある種とんでもない技術のおかげであり、金型屋に甘えていたのです。
それに加え、データ管理なんてExcelで運用できてないから「新規の金型屋の求めるデータ」がすぐに出せないという今までサボっていたツケが移管のタイミングで大きな爆弾になってしまう。
金型屋が少なく、リソースが空いてない工場ばかりなのに、やっとの思いで「対応してくれそうな金型屋」を見つけても、どの金型屋も「このメーカー管理できてないからやばい」「相手にしないほうがいい」と逃げていくのです。
移管不可が嫌なら金型管理を見直せ
金型屋の減少で間違いなく訪れる、懇意に金型屋の廃業、その先には金型移管先を見つけなければならない宿命が待っていますが、移管不可が嫌なら今すぐ金型管理を見直すべきです。
夏休みの宿題と同じで2日前のやばくなってから手をつけてももう手遅れであり、残っている希少な金型屋はどんどん他のメーカーに奪われるので、早く動かないと手遅れになるのは間違いありません。
やるべきことはExcelのその場限りの適当な管理をするのでなく、正しい金型管理の仕組みを導入することであり、アホみたいに高額な費用なんて正しい金型管理に必要ありません。
ここでは移管不可の最大のトラブルを避けたいメーカーの保全部が導入すべき金型管理の仕組みであるAnyMoldを解説します。
金型管理に必要な機能がオールイン
金型管理の導入に高額な導入費用をかけようとしている保全部は愚か者であり、正しい選択肢を選べば、必要な機能が揃った仕組みを月額数万円だけで金型管理を実現することができます。
AnyMoldでは金型の基本情報から図面、製品写真に至るまで関連情報を一元管理できる仕組みを提供し、Excel管理のような情報がバラバラになり、探す作業が発生することはあり得ません。
メーカーの金型管理の問題点は「本来は1つである金型にまつわる情報が分散された」ことが原因であり、きちんと管理するなら「シンプルに一元管理する場所を作れば」いいだけなのです。
情報が1箇所にまとまっていれば「探す作業」が一切不要になり、スムーズに必要な情報を取り出したり、蓄積したデータを活用し、新たな気づきを得ることだって夢ではありません。
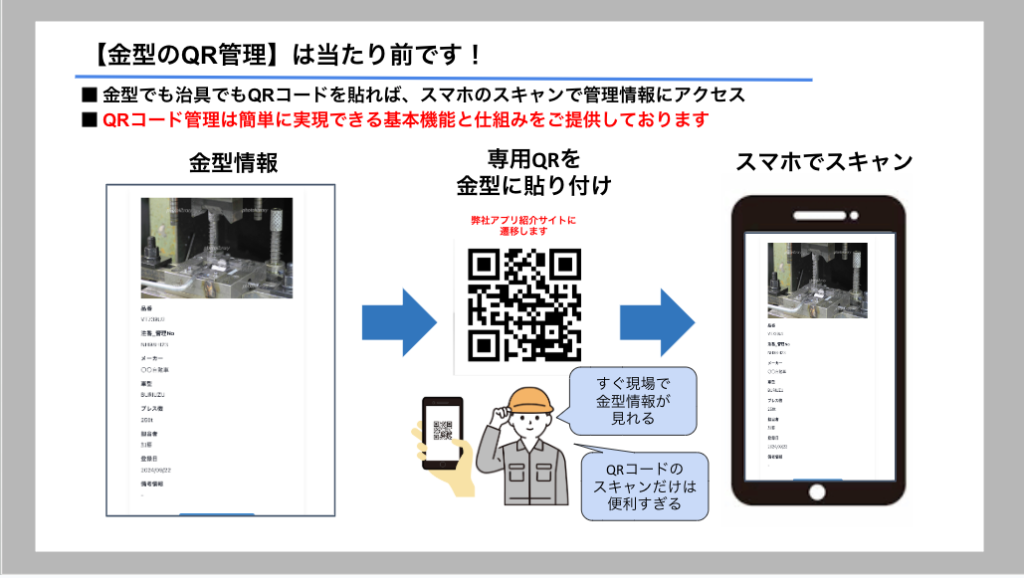
AnyMoldでは金型ごとに管理QRコード作成可能でQRを金型に貼り付けるだけで、スマホのカメラでスキャンで現場でもどこでも金型情報にアクセスできる仕組みを作ることがきます。
QRコード管理は金型管理において非常に作業性を高める仕組みですが、多くのメーカーはコストを気にして手を出していませんが、QRコードなんてテクノロジーを活用すれば無料で簡単に取り組める仕組みなので勿体無い。
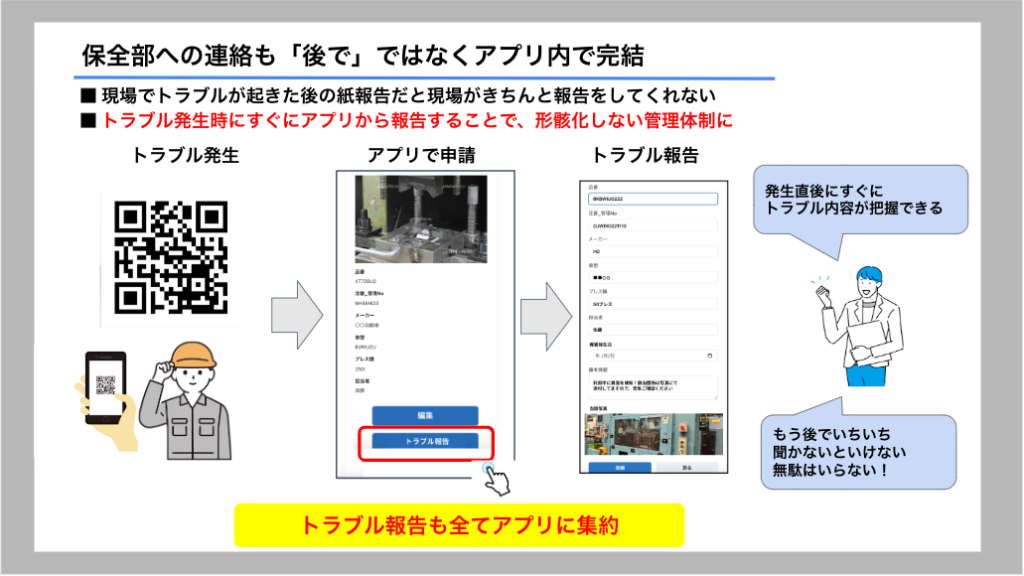
またAnyMoldは「現場からのトラブル報告」もデジタル化に貢献し、従来の紙での事後報告は、現場が紙の報告をめんどくさがって、適切なトラブル報告をしてくれないかと思いますが、このトラブル報告も効率化します。
現場がめんどくさがる原因が「紙報告」にあるなら、紙を書かせずにアプリで報告ができるようにすればいいだけで、「紙を書かなくていい」環境を作れば、現場もストレスなく保全部にトラブル報告をあげてくれます。
- トラブル時に該当金型QRをスキャン
- トラブル内容をアプリに入力して、報告申請する
- 保全部はアプリのトラブル内容を確認し、対応し報告もアプリに。
モノづくりの現場にはめんどくさがりが多く、仮にアプリなどを入れても「めんどくさい」とワガママをすぐ口にしますが、「軍手を外さず音声で話せばいいんだよ」となると現場にも受け入れられやすくなります。
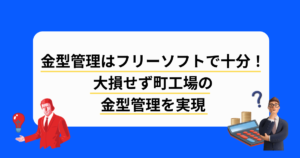
金型に起こる全てを追跡管理
AnyMoldは金型が製造されてから現在までの過程である「故障」「メンテ」「改造」の3つの金型への変化の履歴を全て金型に紐づけて保存できる仕組みのため、1箇所にデータが集まり、データの分断が起こることはあり得ません。
AnyMoldの価値の1つは「データの一元管理」であり、金型にまつわる情報はアプリに全て1ページで管理できるので「Excelを何個も開いて1つ1つデータを見る」ような探す作業はもう必要ありません。
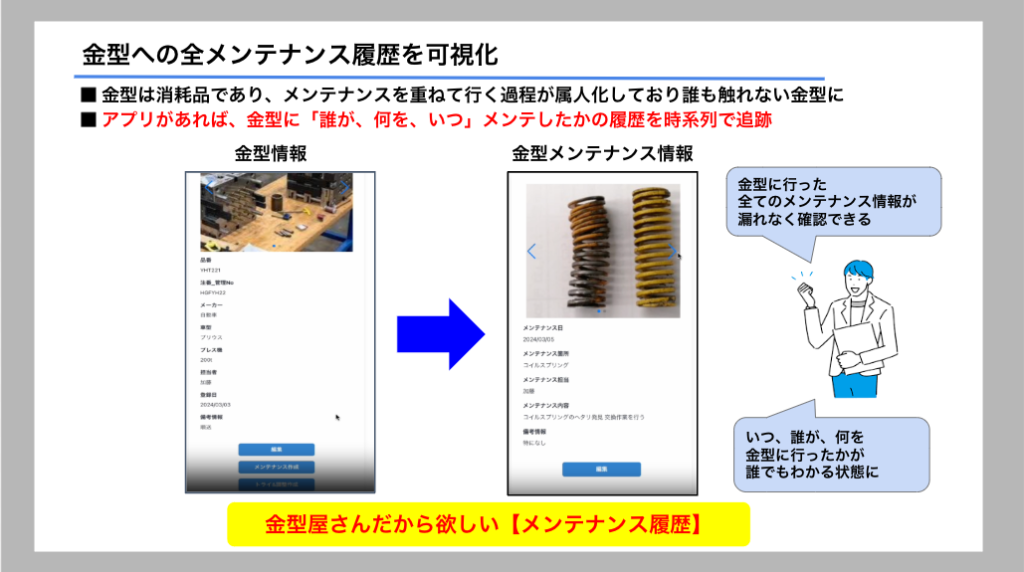
保全部の担当がすぐに知りたい情報や新規の金型会社への金型移管時に絶対に必要となる金型の履歴データはアプリの金型情報と同じページに格納されているので、QRコードを読めば、すぐ確認と提供ができます。
これまで紙やメールで届いていた金型会社からの作業報告、製造現場からのトラブル報告も紙報告の体制のためも別管理が生まれ、データ探しが発生しましたが、関連データを1箇所に集約できるしくみがあれば全部解決です。
管理が形骸化した原因はシンプルで「紙やExcel、メールなどいろいろな媒体で金型に関する情報をバラバラに保管する」せいでデータが分断されてしまったのであり、ただ1つにまとめる仕組みさえ用意すれば保全部は変われます。
AnyMoldは極めてシンプルな仕組みのため、協力会社の金型工場にもメリットがあり、紙でわざわざ書いて提出していた作業報告もアプリに直接入力すれば報告が終わるので、協力会社の手間も省くことができます。
新たな金型会社に金型移管をする際もAnyMold内のデータをPDFやスクリーンショットで抜粋して共有すれば、移管の際に必要な情報提供が済みので、未来の金型移管の仕組みとしても十分機能します。
金型に関する情報がメールや紙、口頭の分断されて報告されていたのは、情報の受け皿となる仕組みが存在しなかっただけであり、受け皿となる仕組みをAnyMoldで用意すれば、メーカーの金型管理は綺麗に機能します。
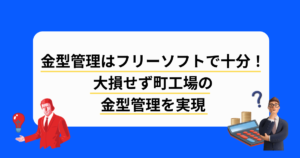
データ活用で保全部が重要部署に
AnyMoldを導入すると、「何か起きる前に動く部署」に様変わりすることが可能であり、その理由はAnyMoldによってデータが整理統合され、蓄積したデータを再利用して、「事前予知の上での保全活動」が可能になります。
導入前はデータがバラバラで探すだけで精一杯だったがAnyMoldで一元管理されていれば、保全部は蓄積データを見るだけで「事前に対応すべき金型」が特定でき、何をすべきかもアプリで気づきを得ることができるのです。
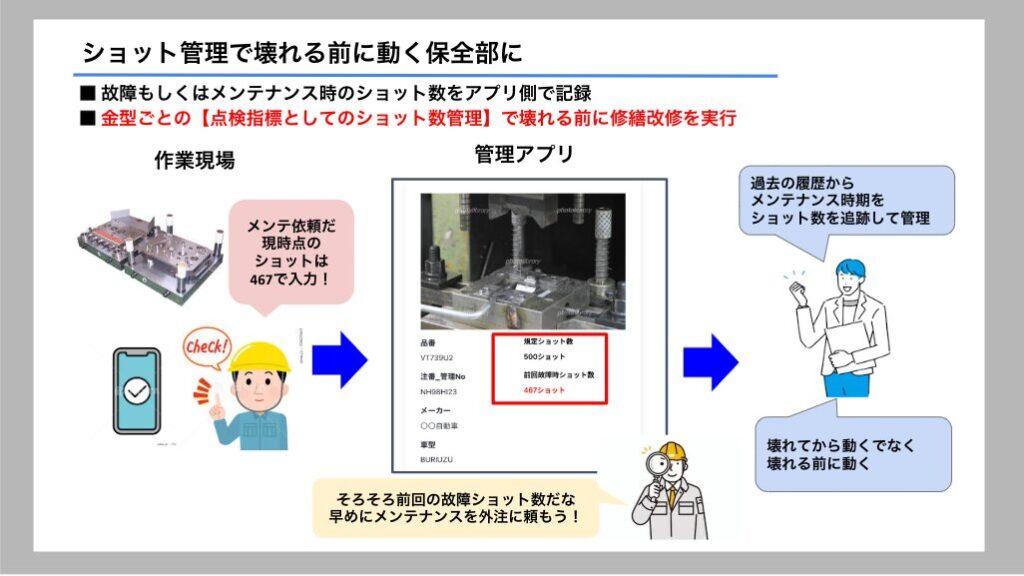
例えば金型のトラブル発生時にショット数を記録する「ショット管理機能」を基本で提供しており、トラブル時のショット数を毎回蓄積することで「金型が壊れるタイミングや目安」を過去のショット数から対策することができます。
蓄積したトラブル時ショット数データから「そろそろ前回のトラブルタイミングのショット数と近いから点検しよう」と蓄積データから事前対策のサインを得て「壊れる前に動く」が実現します。
金型は生き物であり、この先どんなトラブルが起きるかを先読みするのは熟練の職人技でしたが、令和の時代は勘に頼るのではなく、過去のデータを頼りにすれば、誰でも事前予防のきっかけに気づく環境に生まれ変わります。
そしてAnyMoldの導入で保全部は「事前に対処して動く部署」の枠を飛び越えて、新規金型を設計製造する際に過去のデータを活用し、エビデンスを提示することで「壊れにくい金型」の設計に貢献するのです。
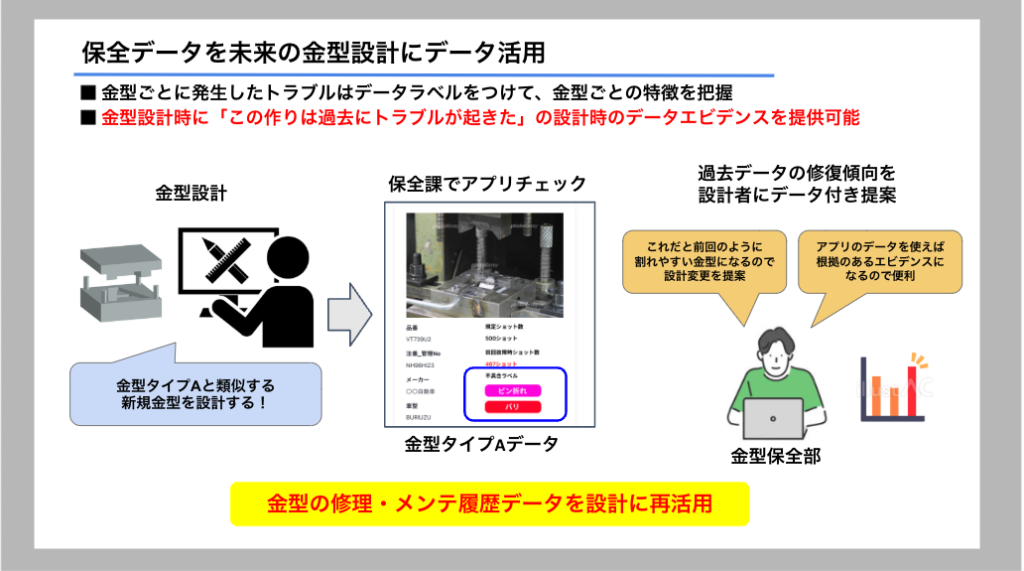
新たな金型を作る際には過去に設計した金型情報を踏襲して設計するケースが多いですが、今までは保全部が対応した故障やトラブルのデータを活用する観点がないので「同じようなトラブルが頻発する金型」が出来上がっていました。
しかしAnyMoldに蓄積された過去のトラブルや修理のデータを共有すれば、新たに設計される金型は同じようなトラブルが起きにくい設計、要は過去のナレッジを生かした金型を設計することができるのです。
設計部は事務所で図面を書くのが本業で、自分が設計した金型が日々、現場でどのようなトラブルや修理が起きているかの全てを把握は不可能ですが、AnyMoldに蓄積されやデータを設計部が提示すれば、設計部は大喜び間違いなし。
設計チェックにおける指摘への回答には「エビデンス」が不可欠で過去の修理やトラブル履歴を明示できる仕組みによって設計部からの保全部の価値は大きく上がり、故障しないの金型のおかげで保全業務も減りWin-Winになります。
ただ保全活動をするのではなく保全業務で得た金型の知見データを上流の設計に共有し、設計をする際には保全部が提案・相談をする環境になれば、保全部の存在意義は向上し、モノづくりの上流から活躍する保全部となるのです。
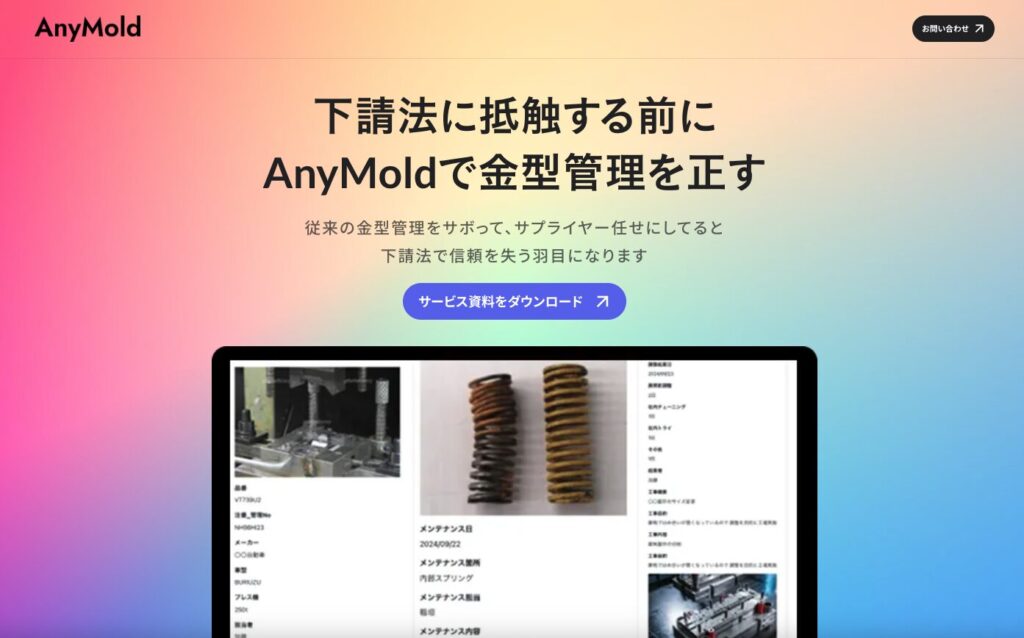
まとめ:金型会社の絶滅にAnyMoldで備えろ
この記事では金型屋の倒産を指を咥えてるメーカーは、いずれ誰も自社の金型の面倒を見てくれず、移管しようにも管理が杜撰なせいで金型会社が誰も相手にしてくれない状態になる点と悲劇を避ける方法を解説しました。
金型会社は今後、絶滅危惧種の存在になることは間違いなく、数は増える可能性はゼロであり、むしろ金型屋の数は団塊の世代が高齢化を迎えて、廃業数が右肩上がりに増えることになるでしょう。
まだ、懇意にしている金型屋があるからと指を咥えて何もしないでいるメーカーは間違いなく、リスクの爆弾が爆発し、金型の移管ができずに途方に暮れることは間違いありません。
これだけ確証を持っていえるのは弊社にも大手メーカーを中心にAnyMoldの問い合わせが増加しており、形骸化した金型管理に危機感を持っている保全部様の声を聞いているからです。
AnyMoldは製造業のあらゆるメーカーの保全部様の声を形にした仕組みですので、ぜひExcelで管理をしている方は検討してみてください。
弊社は製造業のメーカーが下請法に抵触しない金型管理に特化した仕組みである「AnyMold」を提供し、メーカーの形骸化したExcelでの金型管理を解決する支援をしております。
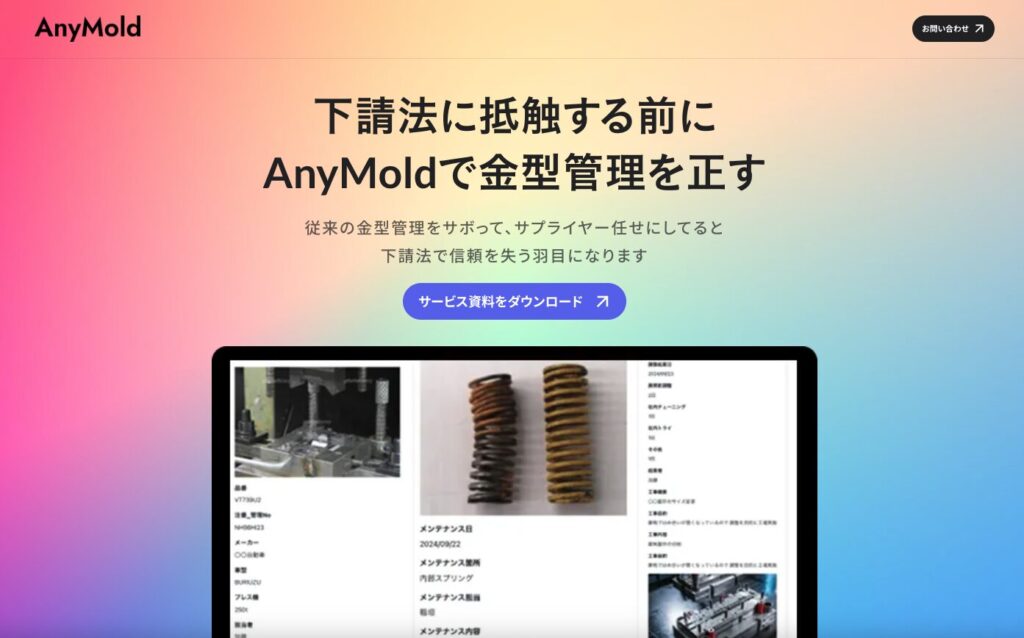
「Excel管理から脱却したいけど何から始めるべきかわからない」「なるべき低コストでデジタル化したい」などのお悩みを抱える方はぜひ資料請求にてサービス内容をご確認ください。
